經理人x Maxxis
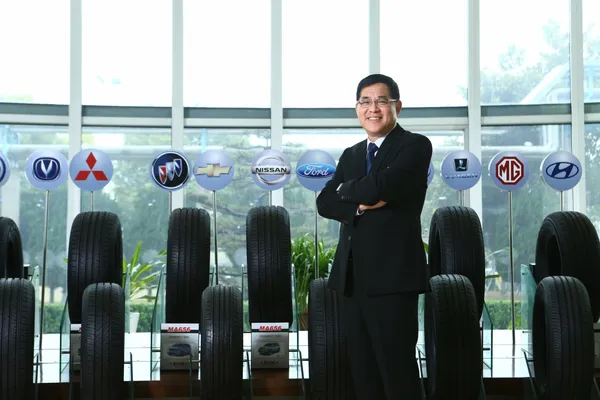
不用開燈、全自動生產,正新瑪吉斯輪胎導入工業4.0,顛覆傳產工作想像,讓人才發揮最大價值
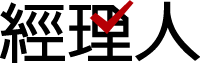
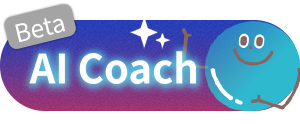
瑪吉斯輪胎在20年前就早已到大陸設廠,正新橡膠(中國)有限公司總經理李進昌邀請我們走進正新昆山廠,原以為會看見勞力密集又黑沉的場景,想不到眼前的景象,讓眾人都跌破眼鏡。
一個人也沒有!一點異味都沒有!這真的是一座輪胎工廠嗎?我們在中午11點來訪,整個車間只有喀拉喀拉的機器不斷運轉,地板乾淨,沒有粉塵,也聞不到工廠常有的異味。瑪吉斯的工廠完全逆轉編輯團隊對輪胎製程廠房的印象。
工作不開燈!? 直擊最「聰明」的輪胎廠
驚喜不只如此,抬頭一看,廠房天花板的日光燈竟是關著的!從屋頂天窗引入的自然光,灑落在機器手臂上,從台灣彰化誕生的瑪吉斯輪胎,正在透過工業4.0--以智慧型系統讓傳統產業快速轉型,現已成功進入「關燈生產」,沒有人,當然不必開燈!代表是相當成熟的工業4.0產業。
昆山廠從混練、押出、成型、硫化、檢測,再到最終入庫,所有步驟幾乎都由機器代勞。從前員工常要開拖車將輪胎搬運到加硫廠房,再放在加硫機上,如今經過成型處理的輪胎,會經由輸送帶自動移往加硫廠房、加硫機,再自動進入下一製程。
「瑪吉斯要在2026年以前躋身全球前5大輪胎廠!」李進昌回憶起2017年,董事長羅才仁定下的目標,帶動旗下各工廠的智慧轉型,從目前的半自動化朝向全自動化生產,昆山廠是其中速度最快的一家。
「Maxxis瑪吉斯」品牌成功心法:是追求產品性能與品質穩定,為此不惜耗時5年、斥資1.5億美元,「Maxxis瑪吉斯」重本打造全亞洲最大輪胎測試廠,爭取國際曝光提升品牌力,並善用兩岸三廠的分工策略,延續正新半世紀的品牌文化、整合產業生態鏈,過程中拋開傳統產業的生產枷鎖,成為全球在地化策略的成功範本。
當然,這樣的成功絕非一蹴可及。早在2002年,正新昆山廠就導入RFID+條碼自動化管理系統。
為何要導入RFID+條碼管理?李進昌解釋道:RFID+條碼是輪胎的「履歷」,就像人的身份證,應用在生產過程中材料與生產參數的管控,可以避免用料錯誤的狀況,例如:應該投A料卻投成B料、確保材料先進先出和落實鮮度管理。RFID+條碼可以紀錄輪胎在生產過程中使用的材料、生產參數、品質檢測結果及性能等資訊,當輪胎出廠後若有任何問題,只要透過RFID+條碼就能回溯整個生產過程。輪胎的品質必須做到安全無瑕疵,才能保障使用者的生命安全。
別再叫我傳產:4大自動化,快速站上產業NO.1
RFID+條碼自動化管理系統上線後,昆山廠開始快速著手改造生產設備,賦予其「自動化」的能力,不僅解決長期面臨的缺工問題、減少人為的影響,大大增加生產效率和穩定性。此外產線自動化後也有助高效管理,可以讓良率提升、製程縮短、減少工安意外、甚至降低離職率。
昆山廠的自動化改造分為4大步驟,從「單機」設備自動化、檢測作業自動化、串連自動化到倉儲物流自動化,最後再透過網連化,將這4道自動化程序串連起來,由中央電腦自動派送生產參數,例如:溫度、RPM、壓力、時間等,改變過往由作業員親自在操控面板上設定條件,並將實際上的數值反饋回電腦,進一步累積成大數據,作為未來導入人工智慧應用的基礎。
導入工業4.0後的正新,成功降低60%人力需求,不只解決缺工問題,也因人力需求由作業員轉向管理人員,使得招募人才更容易更有彈性;其次則是提高品質且確保品質的一致性,間接提高客戶滿意度;最後則是降低生產成本,包含人力、廢料、不良品損耗、能源使用……等。
20年前,被集團派駐大陸的李進昌,志在打造一座中國最好的輪胎廠,20年後,瑪吉斯輪胎中國昆山廠成功智慧大轉型,下一個10年,將為躋身全球前五強集團目標持續邁進。透過工業4.0轉型,Maxxis瑪吉斯輪胎將MIT推向世界之巔,已成為許多國際新車大廠如賓士、BMW、VW、GM、福特、豐田、本田、日產、三菱、现代等新車配套輪胎,產品性能不輸國際大廠甚至更勝一籌,這是許多傳統產業不曾想過的金字塔頂端之夢。