整理·採訪·撰文 邵蓓宣、高士閔
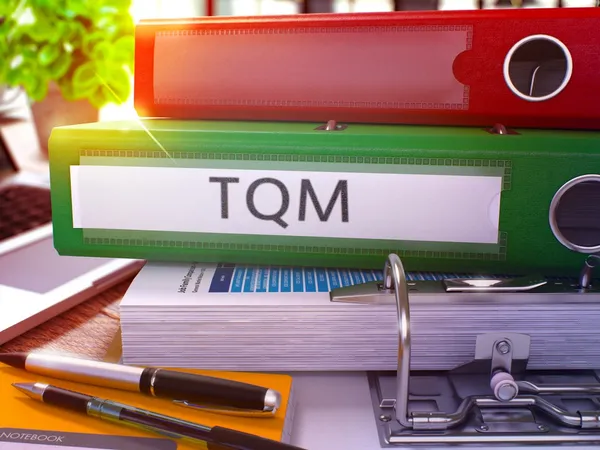
想導入全面品質管理、豐田生產方式?管理大師許士軍:不是每個組織都適用
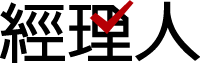
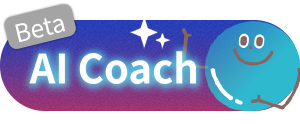
(本文出自《經理人月刊》2017年8月號,封面故事:管理學100年一定要懂的10個經典理論)
如果你是一家汽車工廠的經理人,公司正受到經濟不景氣的影響,業績下滑。你的老闆剛從美國考察回來,看到美國的汽車工廠以量化生產、降低成本的方式發展,要你跟著改善製造流程,並訂下「3年後要趕上美國企業」的目標,你會怎麼做?
這是前豐田汽車(Toyota)副社長大野耐一(Taiichi Ohno)面臨的狀況。
日本在二次大戰後,百廢待舉,而美國自1920年代發展裝配線分工制度後,在1960年代左右開啟了一片天,尤其是汽車產業,3大汽車公司通用(GM)、福特(Ford)、克萊斯勒(Chrysler)成為全球的領導者。但若要完全師法美國式的生產方式,首先面臨的困難就是日本的市場不如美國大。市場不夠大,大量生產以降低成本的方式顯然不適用。為了達成老闆交付的任務,大野摸索出豐田生產方式(TPS,Toyota Production System)。
「我們所做的,其實就是注意從接到顧客訂單到向顧客收帳這段期間的作業,藉由移除能創造價值的浪費,以縮短作業時間。」
學者、專家怎麼看?
逢甲大學講座教授許士軍觀點:「品質」還需納入服務價值
全面品質管理、豐田生產模式為什麼會紅?因為日本商品在80年代全面攻占美國市場。它們的產品又便宜,品質也好,所以消費者全部跑過來。美國企業就很好奇,為什麼他們能這麼便宜,後來才發現全面品質管理,就是一直找哪裡有浪費,把這些錢省下來,反映在價格上,所以能提供低價高品質產品。
以前所謂品質好,是說價格便宜又堅固耐用;但現在品質好,是指能幫消費者解決問題。 像消費者買iPhone不只是看這隻手機的品質而已,還能安裝很多不同功能的應用程式,這些是無形的服務、品牌價值,單純的品質與價格要求已不敷使用。
全面品質管理對需要標準化作業程序(Standard Operating Procedures)的地方還是管用, 但在高度彈性組織裡就不合用了 。如Google每天要面對的事千變萬化,工程師面對的問題更多更雜,也會在不同地方處理工作,企業根本沒有辦法管控每一個人處理每一個細節的步驟。
前富士康副總裁程天縱觀點:時刻思考改善,也別忘了改善的目的
全面品質管理的核心:任何事情都可以被流程(Process)化,所以可以透過科學方法量化目標,進而改善。但使用時要注意, 一定要釐清「為誰而戰?為何而戰?」
舉個例子你就能了解,我在1987年時曾安排台灣一位大客戶造訪惠普(HP)總部,這位客戶因為是人資出身,所以表示希望能跟惠普人資單位座談,互相學習。怎知我致電惠普總部後,惠普副總裁的祕書跟我說:「副總那時有非常重要的品管圈會議,所以時間衝突了!」我就問:「會議主題是什麼呢?」沒想到對方竟然回答:「如何增加與客戶接觸的時間,以提升客戶滿意度。」
我啼笑皆非,客戶都已經到他眼前,卻因為要開會而沒辦法跟客戶見面,真是本末倒置。這就是全面品質管理最大的問題,這個理論經過多年持續不斷的改善,很容易讓員工迷失在改善的循環之中,而忘記改善的目的是什麼,導致「見樹不見林」的情況。
資料來源 / 《創客創業導師程天縱的經營學》,商周出版
全面品質管理詳解
檢視8大過剩產出,消除無價值的作業
豐田生產方式就是「消除不必要的浪費」。所謂的浪費,就是產品生產過程中,不能帶給顧客價值的流程。因此豐田生產制度中,第一個要思考的問題就是:「顧客希望從這個流程中獲得什麼?」
《豐田模式》將製造流程中未能創造價值的浪費歸結出以下8種:
1.生產過剩
大野認為,生產過剩是最根本的浪費,因為這會導致其他環節的浪費。製造流程中若任何步驟的生產超過顧客所需要的數量,就會導致上一個流程的存貨量增加。
2.在現場等候的時間
如果員工只是在一旁看著機器有無出狀況,等待下一個處理步驟,或因為機器設備停工、出貨延遲而在旁等待,都是人力資源上的浪費。
3.不必要的運輸
進出倉儲,或在流程之間搬運原料、再製品,都是時間和內部資源的消耗。
4.過度處理或不正確的處理
採取不需要的步驟,因為工具或產品設計不良,導致不必要的加工。
5.存貨過剩
堆放用不到的成品、半成品、原料,不僅會占用倉儲空間,若放置太久,也會折舊。
6.不必要的移動
員工在執行任務的過程,任何不必要的動作,像是尋找貨物、前往取貨處等等。
7.瑕疵
產出瑕疵品就必須經過修改、重做、報廢、檢驗等一連串修補行為,這代表要花更多時間處理問題,卻無法帶來新產值。
8.未能被使用的員工創造力
沒有傾聽第一線員工的建議,無法善用員工的才能與技巧,使員工失去改善工作為公司提供貢獻的機會,也屬於一種人力浪費。
「及時化」「自働化」兩大支柱,浪費無所遁形!
要解決上述浪費,大野在《豐田生產方式》指出,應把下列兩大項工作觀念貫徹其中。第一為「及時化」(Just in Time),第二是「自働化」(Jidoka)。
「及時化」就是即時生產,在組裝汽車的過程,所需的裝配零件都是提供剛剛好的量、能即時在生產線旁領取,也就是說,所有生產線上配件的使用是一個接一個,庫存接近於零。
要做到零庫存,等於是顧客下單才生產,有一個需求才有一個步驟,這就產生了所謂的「後拉式制度」,需要補貨或製造時,再向前一個製程發通知。
「自働化」則是指在生產線上裝上自動檢查器,如果發生異常會自動停機,以燈號或警示音等訊號通知異常。
為了讓作業流程中每個環節更精準快速地傳達所需配件,豐田生產現場也產生「看板」制度。員工可以透過大型「看板」,對於所需零件的號碼與數量,以及領取、搬運或生產的相關指示一目了然。
遵照下一個製程的需求作業,做到即時生產
追溯豐田「及時化」的概念,其實是汲取美國統計學家、質量管理學家威廉‧戴明(William Deming)的全面品質管理(Total Quality Management)。
《20世紀80年代管理思想》中提到, 所謂的全面品質管理,原則上就是不允許交貨延遲、交貨差錯,以及交出有缺陷的產品,從一開始就控管產品質量,不要想著靠後期的檢驗去保證品質。
《豐田模式》也提及,戴明在日本舉辦的「美國品質與生產力研討會」中提倡,在一事業體系中,達成或是超越顧客的期待,是組織內每一個人的責任。戴明還把顧客的定義擴大為外部顧客和內部顧客。
外部顧客就是買你產品或服務的客人;內部顧客,就是生產線上或作業流程中的每一個人或每一個步驟,尤其是上一個流程,你要在正確的時間供應他(它)所需要的東西,換句話說,下一個流程的人或物,就是你的顧客。
戴明的原則,其實就是即時生產最重要的概念,因在後拉式的制度中,前一個製程必須遵照下一個製程的需要和指示作業,否則,很難做到即時生產,又不延誤交程期限。