Y Chen
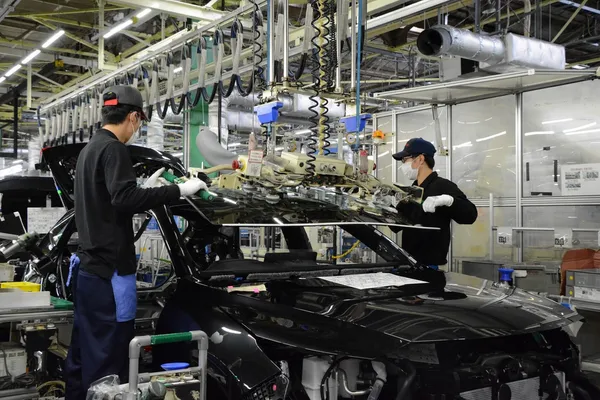
車用晶片荒,豐田汽車為何沒在怕?各大車廠都斷鏈,它靠這個管理法穩定開工
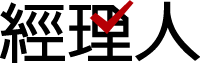
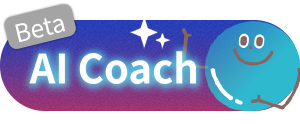
一場大火,讓全球原本供應就不足的車用晶片,燒出更大缺口。全球第三大車用晶片供應商瑞薩電子(Renesas Electronics)位於日本的工廠,在 3 月中發生火災,對於各大車廠而言,是繼今年 2 月美國德州大停電後的另一大打擊,導致現代汽車、日產汽車等多間車廠產線可能都得喊停。
這次鬧出晶片荒,除了供應商受到外部不可抗力因素,多數廠商秉持「及時生產」、沒有庫存晶片的習慣更是主因。
然而,身為及時生產、零庫存始祖的豐田汽車(Toyota),比起眾多車廠,不僅受到的波及較小、甚至還能穩定開工,「及時生產」這套已經有 70 多年歷史的生產方法,究竟在豐田汽車內部出現了那些改變?
311 大地震等天災導致供應鏈停擺,迫使豐田汽車重新審視生產流程
時間回推到 2011 年、日本發生了死傷嚴重的 311 大地震,當時地震不只摧毀一般民眾的生活,更使得許多供應鏈跟著停擺。豐田汽車就在這個時間點,意識到過去的生產管理方法,存在著不小的風險。另外,豐田汽車在 2012 年報中提到,2011 年豐田汽車在泰國的供應商,也因為水患緣故而拖累產能,最終造成該財務年度減產了 24 萬台汽車。
《路透社》(Reuters)提到,經歷了兩次天災,豐田汽車發現半導體供應鏈交貨時間過長,很難抵擋自然災禍,進而要求所有供應商,都必須儲備 2 到 6 個月的晶片。
除了車用晶片之外,豐田汽車還盤點出 1200 多種類似條件的零件與材料,並從中列出 500 多項優先級更高、必須確保能穩定供應的零件,都應該事先儲備好一定數量,以防再次出現缺貨、斷鏈的窘境。
這些做法,被豐田汽車稱作 「業務持續性計畫」(Business Continuity Plan,BCP),不只規定供應商的存貨量,也分散風險較高的零件來源,以及盡可能通用化所有的零件設計。
業務持續性計畫(BCP)讓豐田汽車倖免於晶片荒
BCP 在車用晶片荒中發揮了十足功效,根據《路透社》報導,汽車電子供應商哈曼國際工業(Harman International Industries)的消息來源指出,他們接觸這麼多汽車廠牌,豐田確實是唯一一間能面對晶片短缺問題的企業。
不過,以往豐田生產方式的精髓,就在於消除各式各樣的「浪費」,才能提高效率、縮短產品交付時間,而庫存也是其中一個要縮減的項目。BCP 難道沒有違反這項原則?
「及時生產」的反思:零庫存真的夠精實嗎?
「對我們而言,BCP 是一種經典的精實解決方案(lean solution),」豐田汽車發言人表示,對豐田汽車而言,零庫存只是一種手段,真正目標是透過各種方法,判斷供應鏈中脆弱、有風險或容易受到不可抗力因素影響,導致停擺的環節,並找出相應的解決方法。
從這個角度來看,儘管 BCP 表面上增加了庫存,但卻達到了一樣的目的:確保生產流程順暢,減少產線中止帶來的傷害。
事實上,近年關於豐田式生產強調的「及時」、「精益」等元素,出現了許多討論與反思,尤其自新冠肺炎爆發以來,不同行業也遭遇到類似車用晶片短缺的情況,紛紛被迫斷鏈。《Industry Week》就強調,總是保持最低限度庫存,並不代表一間企業是精實的,與豐田汽車實行 BCP 的出發點類似,關鍵是降低整體生產流程成本與浪費,不該執著於特定手段。
豐田汽車 BCP 給管理者的啟示
那管理供應鏈的方式,究竟該如何調整?擬定和豐田汽車 BCP 相同的計畫,是一條路線。《富比世》(Forbes)也提出另一種解決方案:導入更透明且即時更新的數據管理策略,未來供應鏈應該更頻繁監控庫存與供應商資訊,而非單純覺得「庫存少就是好」,才能及時掌握市場供給與需求,以更快地反應供應鏈的大小變化。
資料來源/Reuters, TOYOTA, Industry Week, Forbes